Compression Thermoforming
Maximum Dimensional Control in Thermoforming
Compression thermoforming is a process that typically uses composite thermoplastic laminates during part formation. During the compression thermoforming process, the preheated thermoplastic laminate is placed in a heated mold cavity. The mold is then closed when a second matched mold applies pressure and causes the material to form around every detail in the mold. Once the molding material cures and cools, the molds are separated.
An ideal manufacturing process for structural parts that require composite laminates, compression thermoforming is more economical compared to the generally high operating costs of transfer molding or injection molding. Compression molding is material-efficient; an important attribute when working with expensive or difficult-to-create composite thermoplastics.
We would be happy to review your drawings or CAD files. Email your WinZip compressed file(s) to fsisales@formedsolutions.com. We accept the following formats:
– NX Native
– Step
– Parasolid
– IGS
– AutoCad 2D .DWG or .DXF

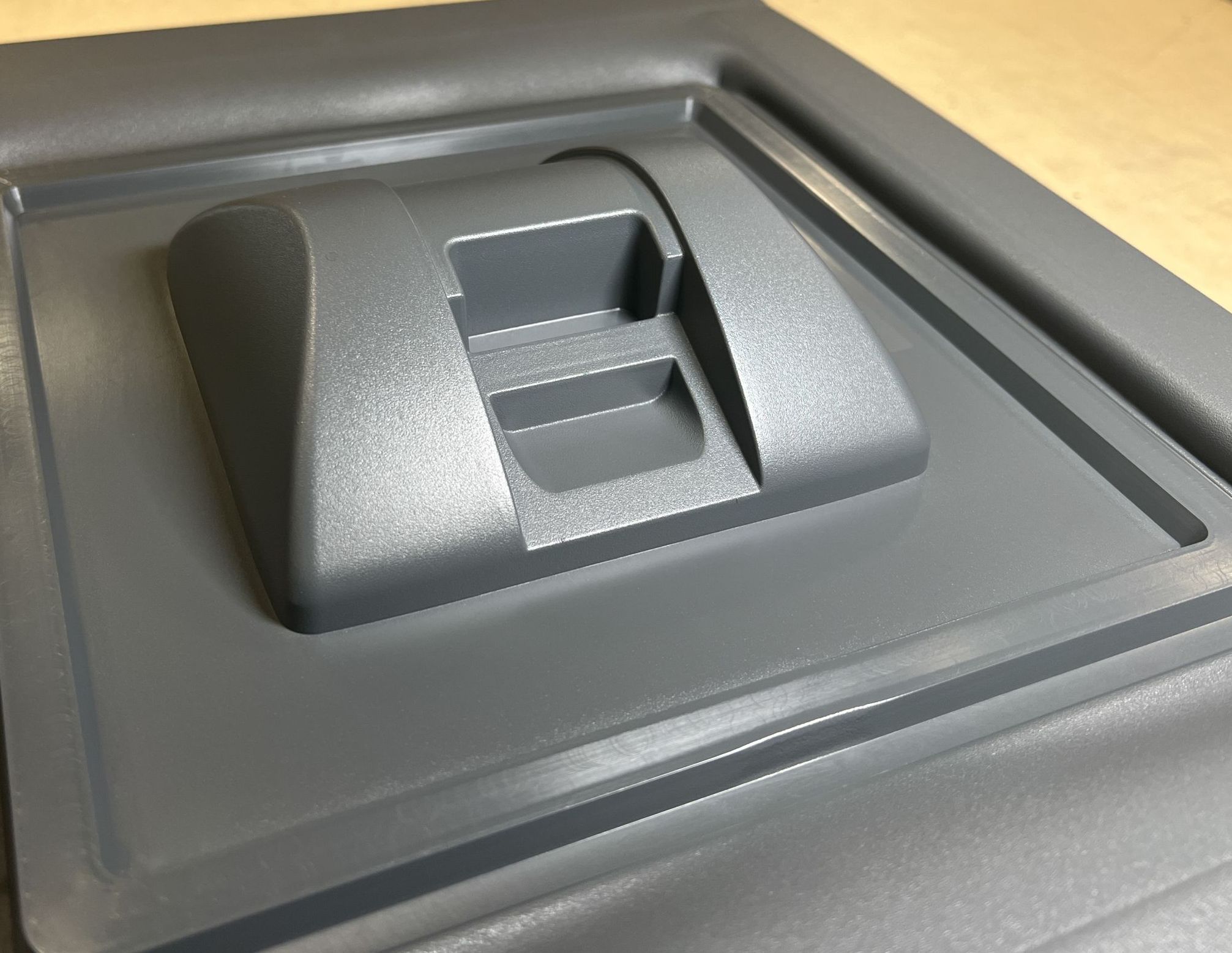
Here are a few key terms associated with compression molding:
Thermoforming:
Thermoforming is a type of manufacturing process in which a plastic sheet is heated and then formed over a mold. There are different types of thermoforming, depending on the needs of a project including vacuum forming (which utilizes vacuum pressure), pressure forming (which utilizes forced air pressure), and compression molding (which utilizes matched metal mold sets).
Composite Thermoplastics:
Composite thermoplastics are highly engineered thermoplastics. These materials allow the composite material to maintain a lighter weight while increasing the strength and durability of the material. Composites are also highly customizable and can be optimized for a wide range of environmental conditions and applications.
Matched Aluminum Mold Sets:
For the compression molding process, two close-fitting aluminum molds are designed and created. When heated thermoplastic is compressed between the two molds, the desired part is formed. Aluminum molds are much more durable than ceramic or wood alternatives and provide a high level of design flexibility.